Alright, let me tell you about this whole acid sump pump situation I had. It wasn’t pretty, and it definitely taught me a few things the hard way. It all started in my workshop, where I sometimes deal with, well, let’s just call it ‘less-than-friendly’ liquids that need clearing out.
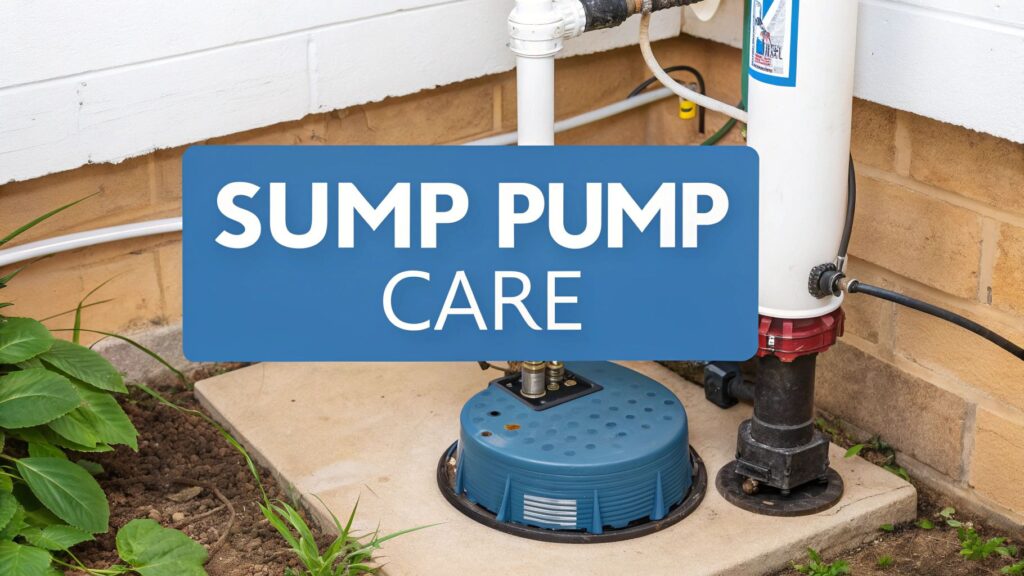
The Mess I Was In
So, I had this collection pit, sort of a sump, where spills and runoff would gather. For a while, I was just using a regular old submersible pump I had lying around. One of those cheap ones you get for emptying a kiddy pool or a flooded basement corner. I figured, water is water, right? Wrong. So very wrong.
Things started to go south pretty slowly at first. The pump would sound a bit rougher each time. Then it started taking longer to clear the pit. I just thought it was getting old, maybe a bit clogged. I even took it apart once, cleaned it, but it didn’t help much. Then, one day, it just quit. Dead. Kaput.
Figuring Out the Real Issue
When I pulled that pump out, it was a mess. The casing, which was some kind of metal, was all pitted and corroded. Looked like Swiss cheese in places. The impeller was practically gone. That’s when the penny finally dropped. The stuff collecting in that pit wasn’t just dirty water; it had some bite to it. Acidic. Not like super strong battery acid, but enough to eat through a standard pump like nobody’s business.
I felt pretty dumb, honestly. Should’ve realized it sooner. My carelessness had cost me a pump and created a bit of a stinky, backed-up situation. Now I had this pit full of nasty liquid and no easy way to get it out.
The Hunt for the Right Pump
So, the search began. I knew I couldn’t just grab another off-the-shelf special. I started looking for something that could handle corrosive stuff. Typed in all sorts of things online, “chemical pump,” “corrosion-resistant pump,” and eventually landed on “acid sump pump.”
Let me tell you, these things are a bit different. They’re usually made of special plastics or stainless steel – materials that don’t just dissolve when they look at something sour. Finding one locally? Forget it. I had to order it online, which meant waiting, while my pit situation wasn’t getting any better.
I spent a good bit of time looking at specs, trying to figure out what I needed. Flow rate was one thing, how fast it could pump. Head height, how high it could lift the liquid, was another. And of course, the materials it was made from. I didn’t want to go through this again.
- Checked the material – had to be something like polypropylene or PVDF.
- Made sure the seals were also up to the task.
- Looked at the power – didn’t need an industrial monster, but something that wouldn’t struggle.
Getting It All Hooked Up
When the new pump finally arrived, it looked a lot more serious than my old one. Heavier too. The instructions were, well, instructions. A bit technical, but I muddled through. The main thing was making sure all the connections were tight and that the discharge hose was also made of something that wouldn’t degrade.
I was extra careful this time. Double-checked everything. I even wore gloves and eye protection, which I probably should have been doing before, considering what was in that pit. Lowered it in, connected the hose, plugged it in, and held my breath.
How It All Turned Out
And wouldn’t you know it, the thing worked like a charm. It was quieter than the old pump ever was, even when new. It emptied that pit faster than I expected. No fuss, no drama. Just did its job.
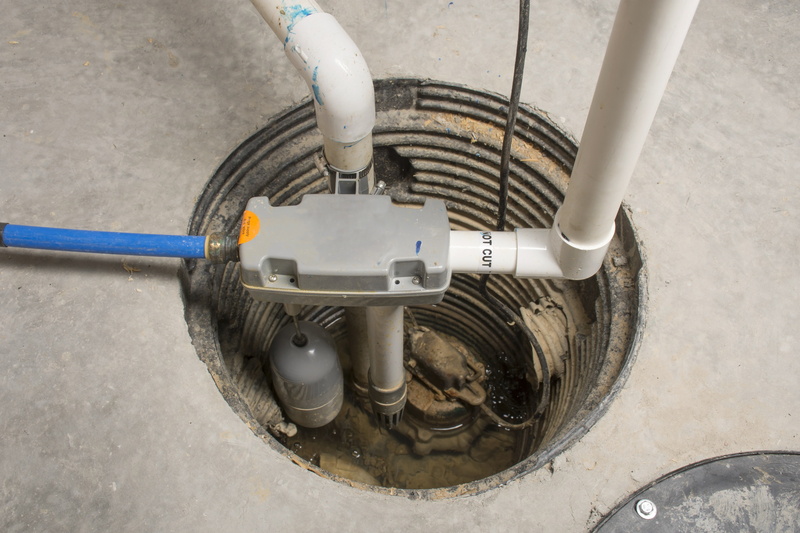
It’s been running for a good while now, and I check on it regularly. So far, so good. It still looks brand new, no signs of corrosion at all. That nasty liquid doesn’t seem to bother it one bit.
My biggest takeaway? Pay attention to what you’re pumping. If it’s anything other than plain water, do your homework. Getting the right tool for the job, especially when dealing with corrosive stuff, saves you a lot of headaches, and money, in the long run. I learned that lesson. Hopefully, someone out there can learn from my screw-up instead of making their own.